自作サイクロン集塵機を改良することにし、前回、インレット管を配管するところまでできました。
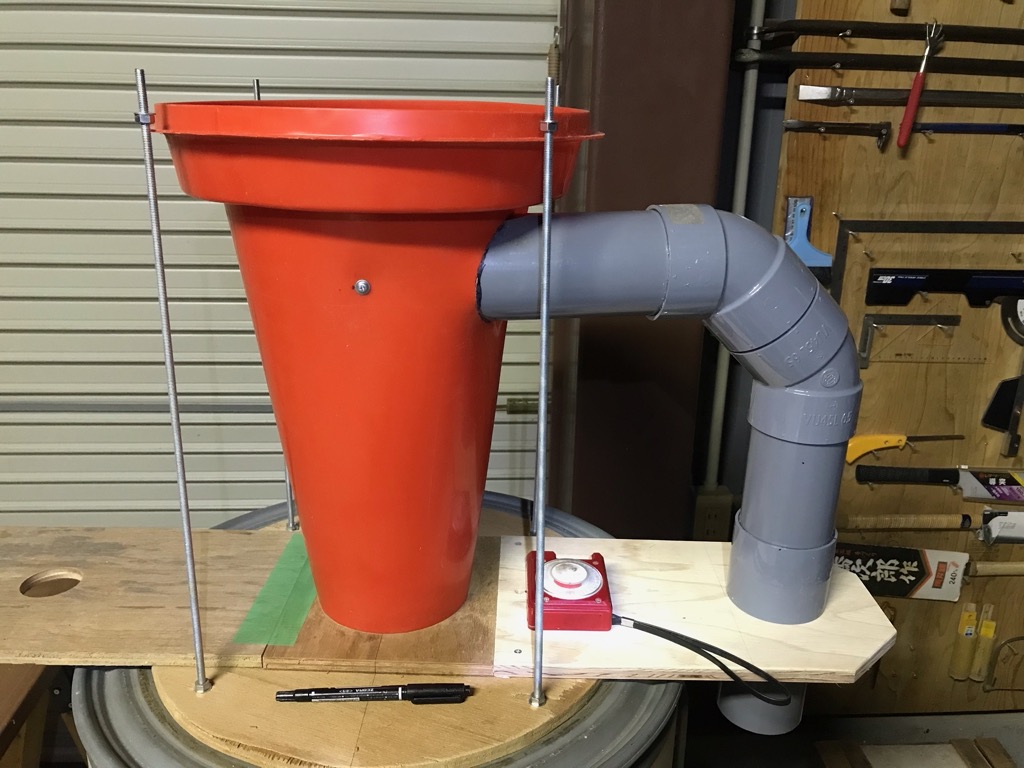
続いて、アウトレット管を配管します。
アウトレット管は下図のとおりサイクロン装置と木工用集塵機とを結ぶもので、口径40mmの塩ビ管(VU40A)を用います。
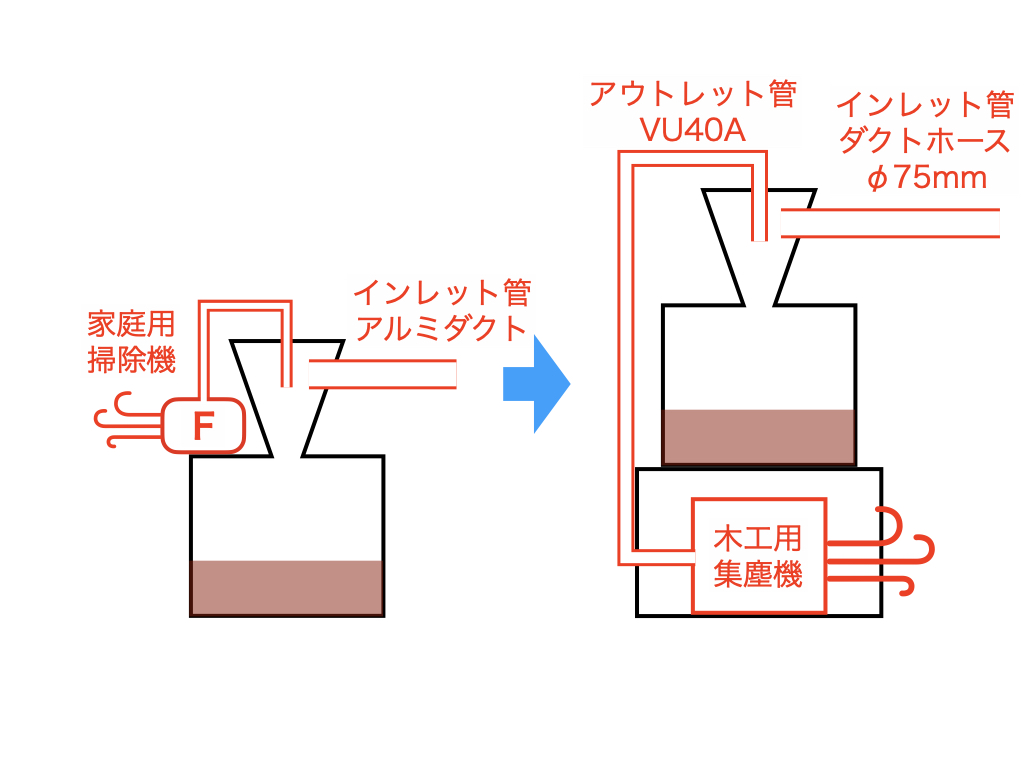
とりあえずサイクロン装置側を配管することにします。
サイクロン装置からの取り出し口は以前もVU40Aを使っていたため、そのまま使えます。
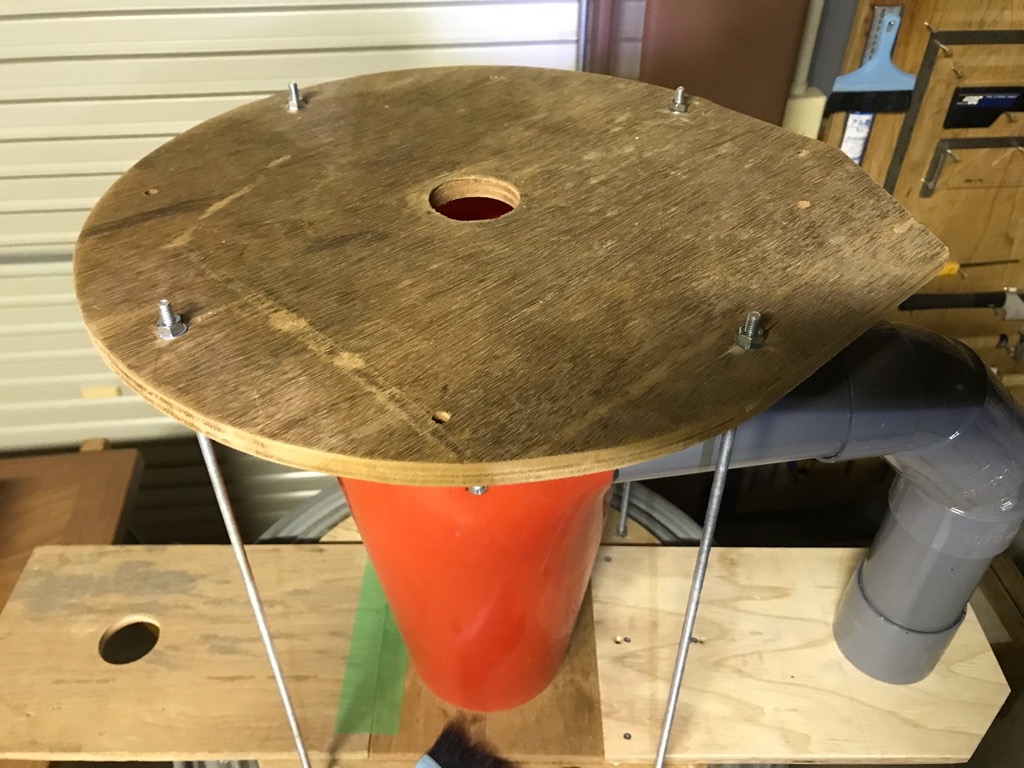
塩ビ管(VU40A)を継手(エルボ、ソケット)使って下写真のとおり組みます。
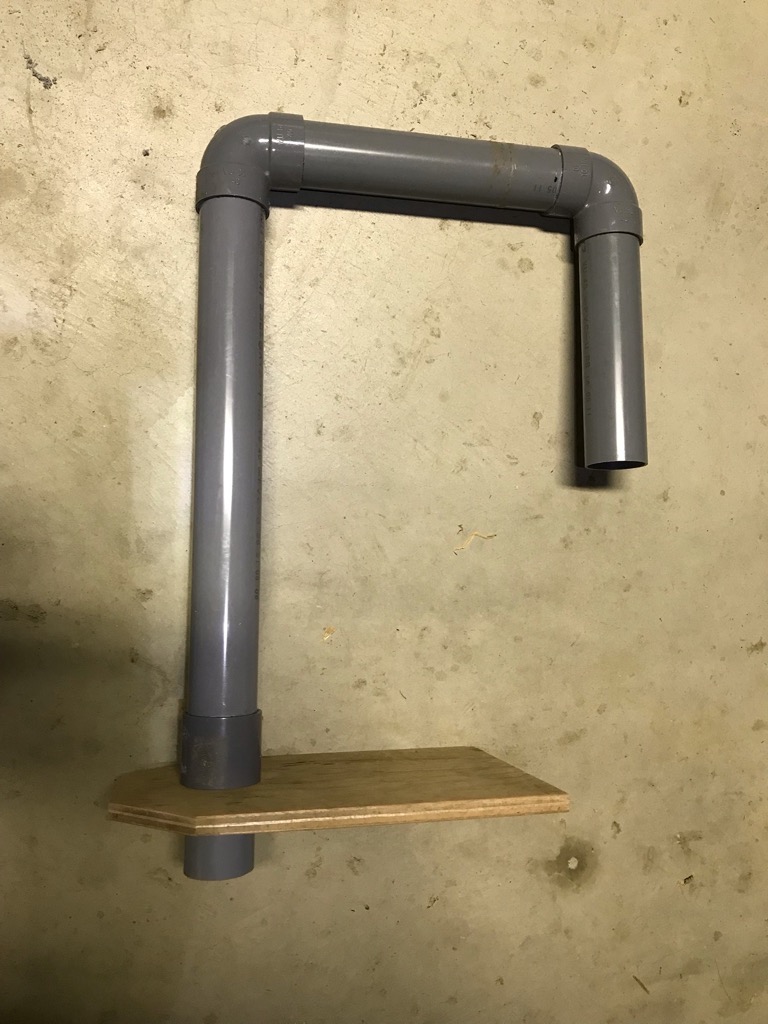
インレット管のときと同様に途中にソケットを入れてアウトレット管を支えられるようにしています。
サイクロン装置に取り付け。
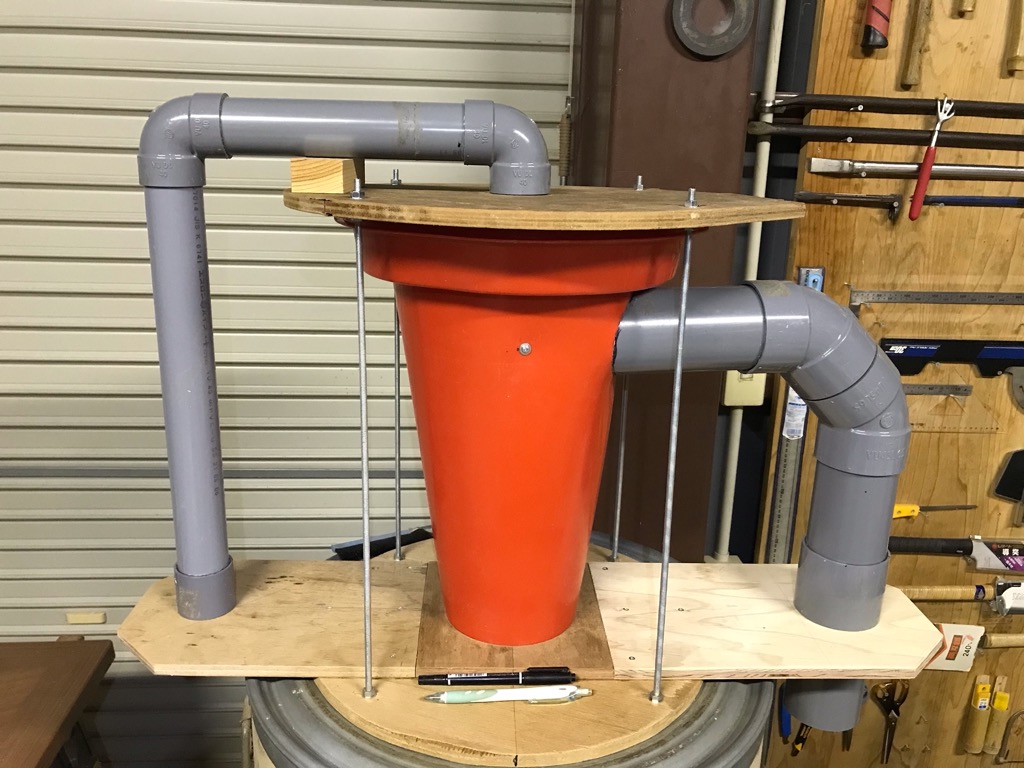
先の支え(ソケットと板)により重力方向については問題ないものの、横方向には安定しません。
そこで、端材を使って下写真の固定具を作製。
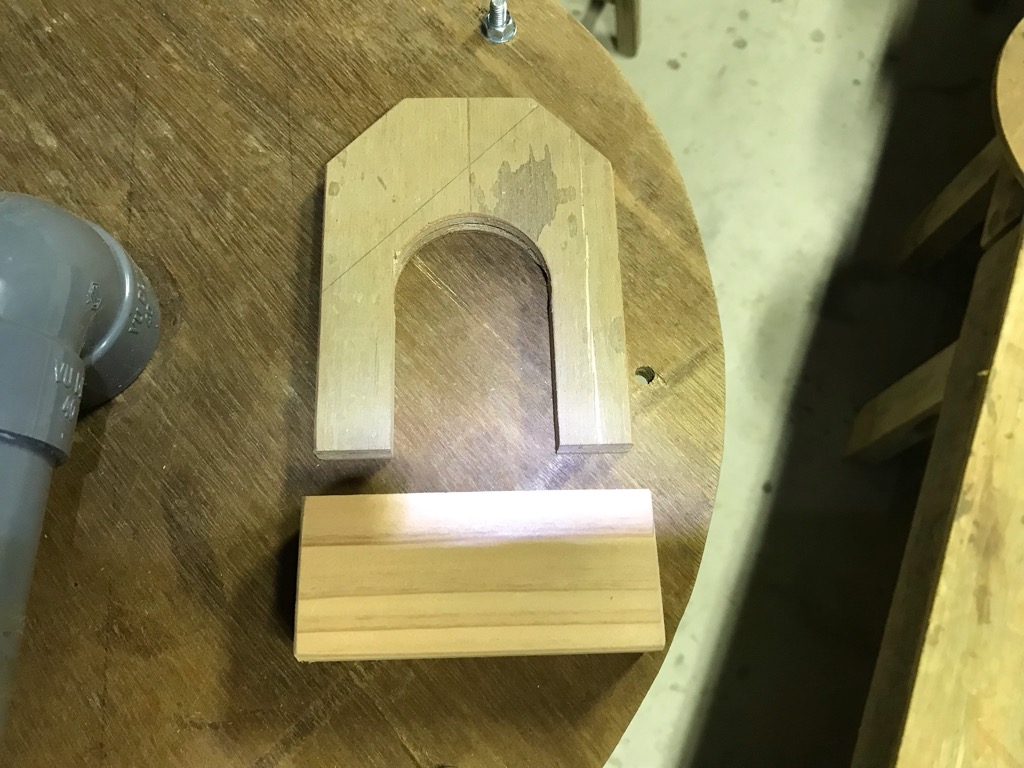
インレット管のほうも同様のものを作ります。
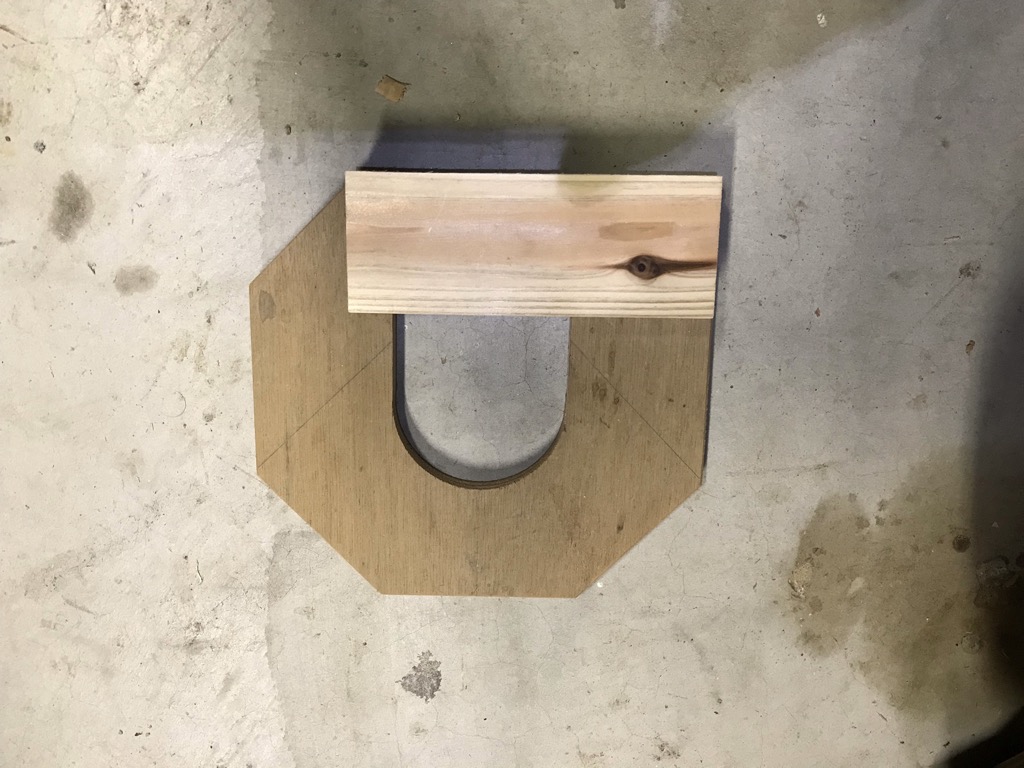
これらの固定具をサイクロン装置の蓋(合板)にビス留めして、インレット管及びアウトレット管を固定。
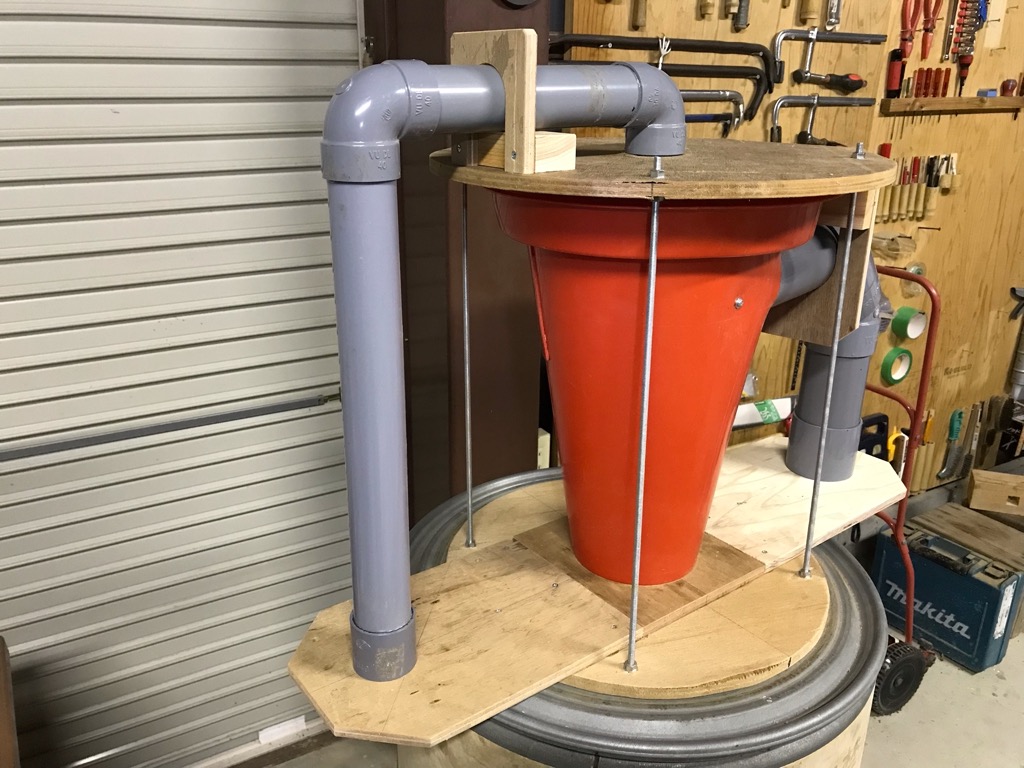
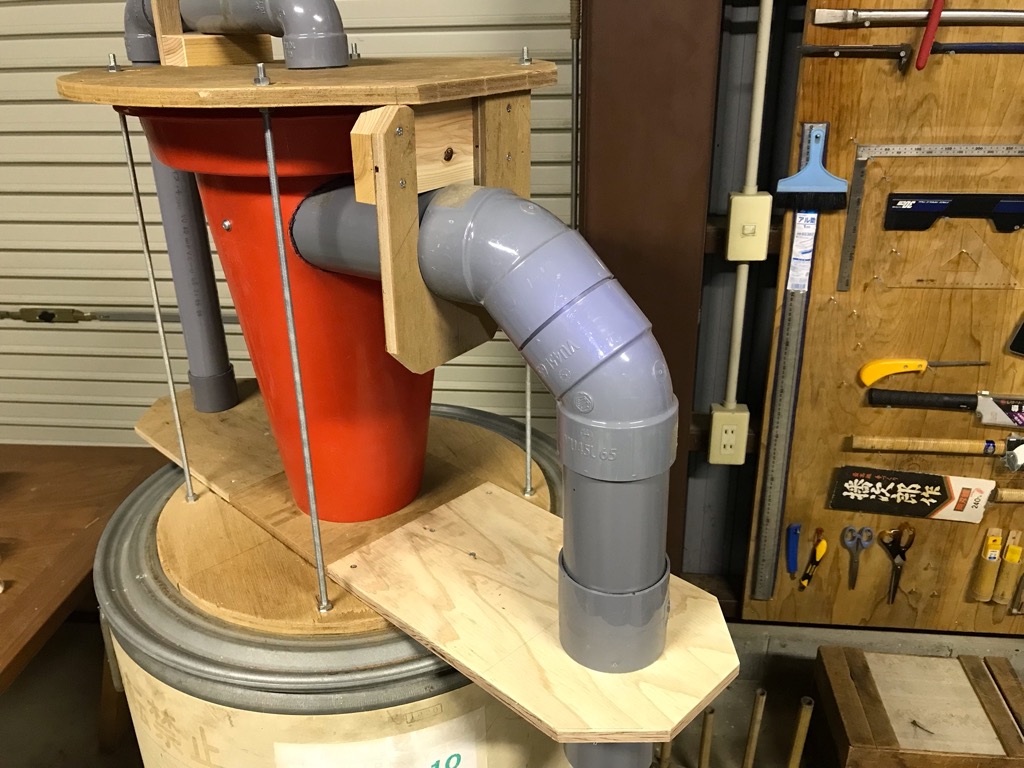
何しろカラーコーンの強度がないため、カラーコーンに余計な力が作用しないようにしておく必要があります。
アウトレット管について、サイクロン装置側ができたため、次に集塵機側を行います。
集塵機側はアウトレット管を集塵機の吸込口(下写真で朱色矢印)接続することになります。
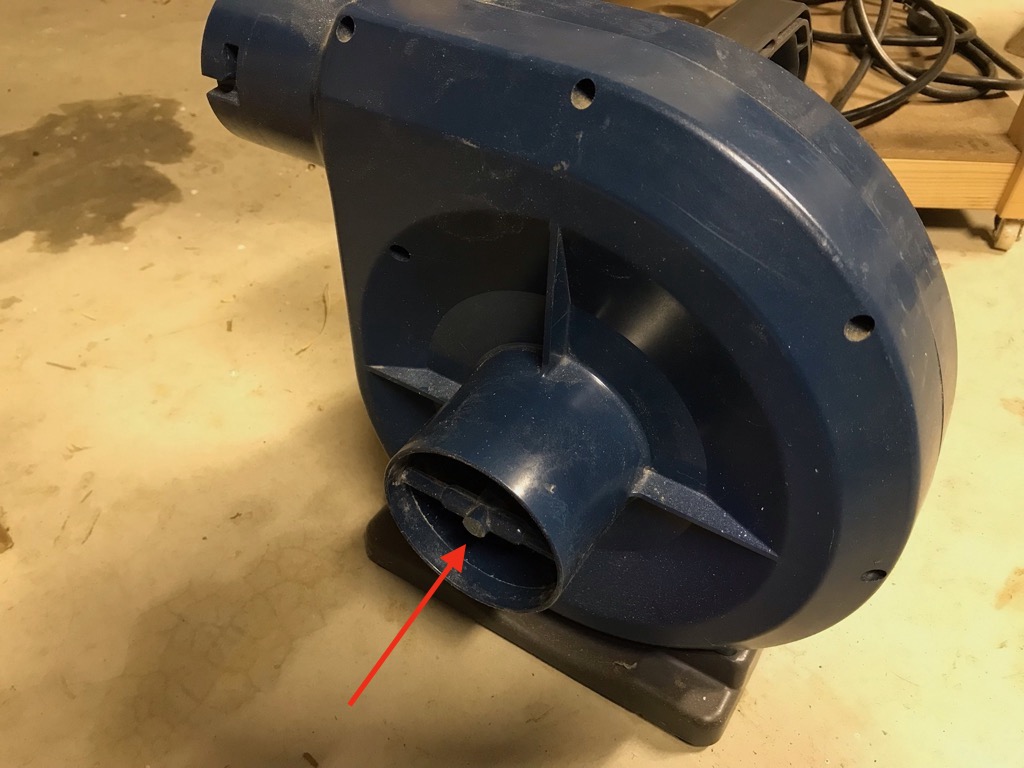
接続には吸込口の内径(76→75mm)から塩ビ管(VU65A:外径76.0mm)を使うことにし、塩ビ管の表面を少し削って薄くし、吸込口に挿し込めるようにします。
また、吸込口の少し奥に横棒が仕込まれているため、それに引っ掛けて固定できるように塩ビ管を加工します。
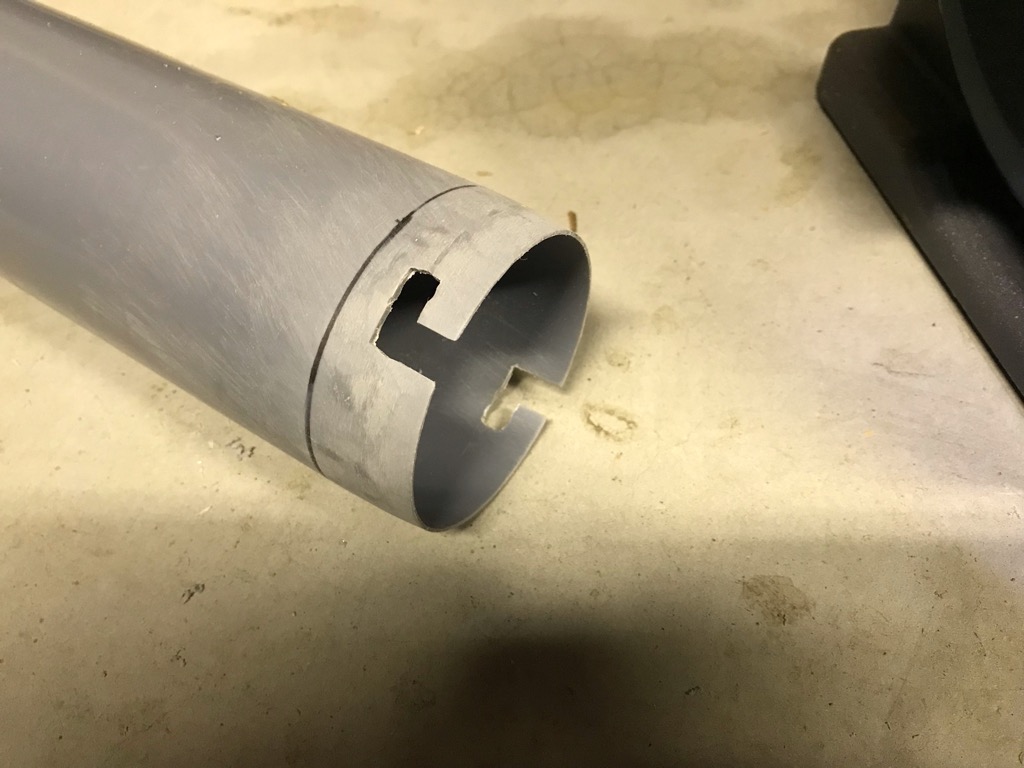
この塩ビ管(VU65A)をインレット管(VU40A)に繋ぐには下写真で左下の継手(インクリーザー:65A×40A)を使います。
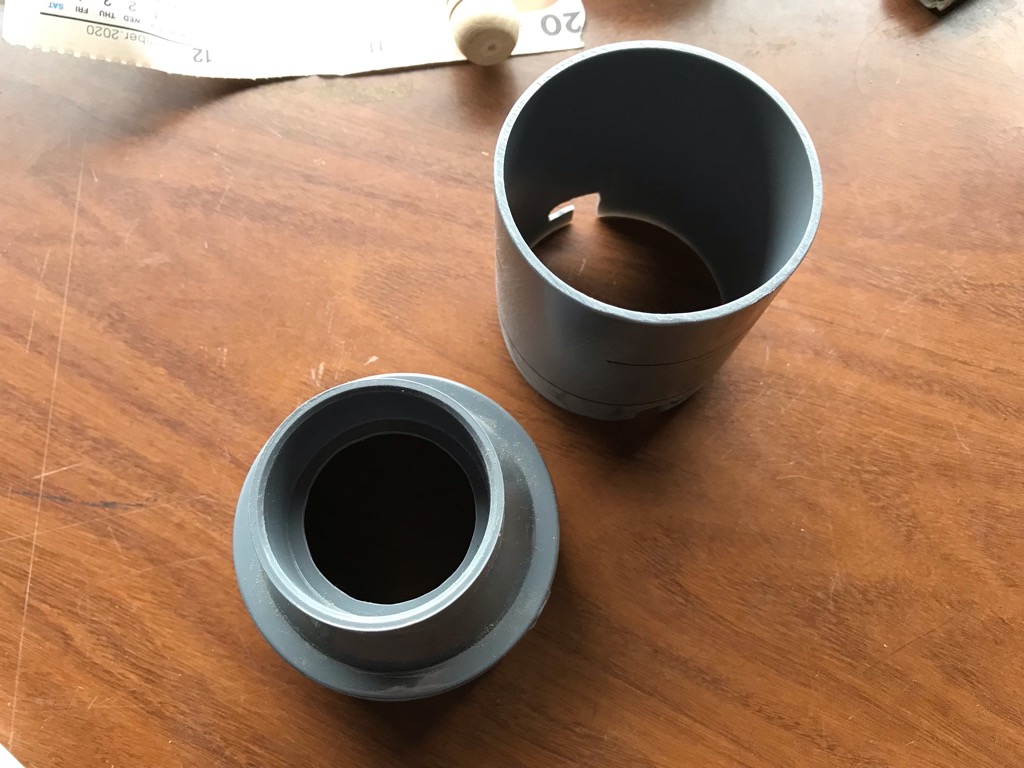
ところで、塩ビ管の継手にはTS継手、VU継手、DV継手の3種類があります。
今回はVU管を使っているためVU継手を使うべきですが、ホームセンターには65A×40AのインクリーザーはDV継手のものしか置いてなく、仕方なくそれを購入しました。
DV継手はVP管用のものですが、VP管もVU管も外径が同じためVU管を接合できます。
ただ、継手の内側にVP管とVU管の肉厚の差(1.8mm)だけ段差が生じるため、その分を削っています(百均の砲丸砥石がここでも活躍!)。
そして、下写真のとおり配管。
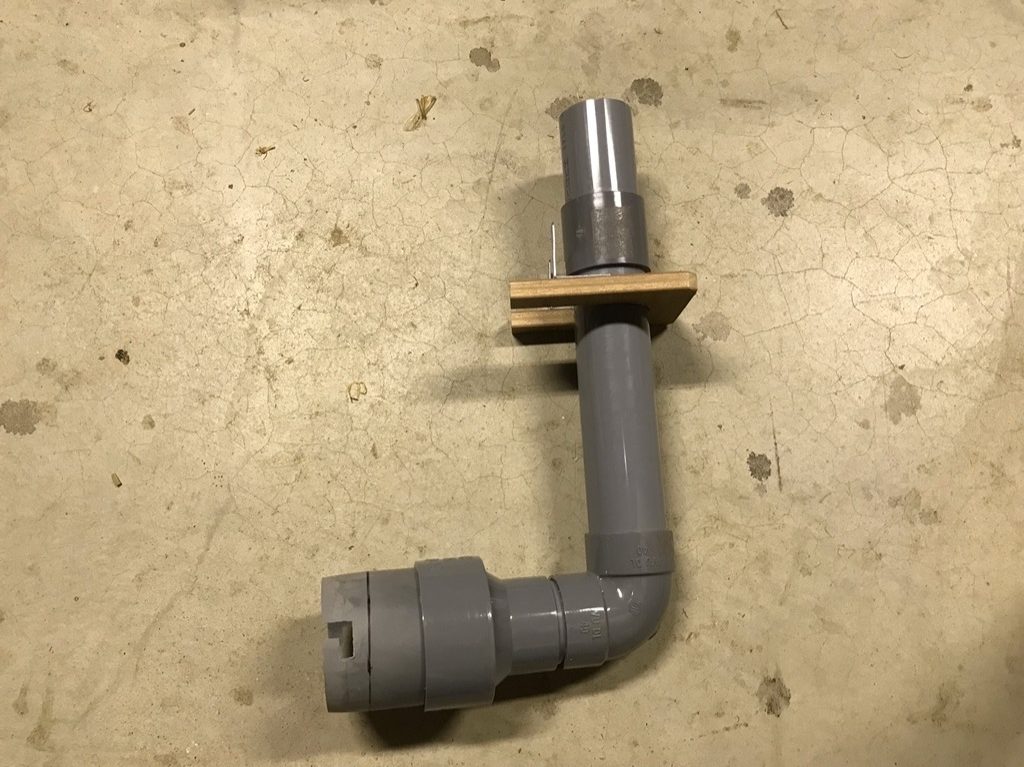
こちらもソケットを入れてアウトレット管を支えられるようにしています。
取り付け。
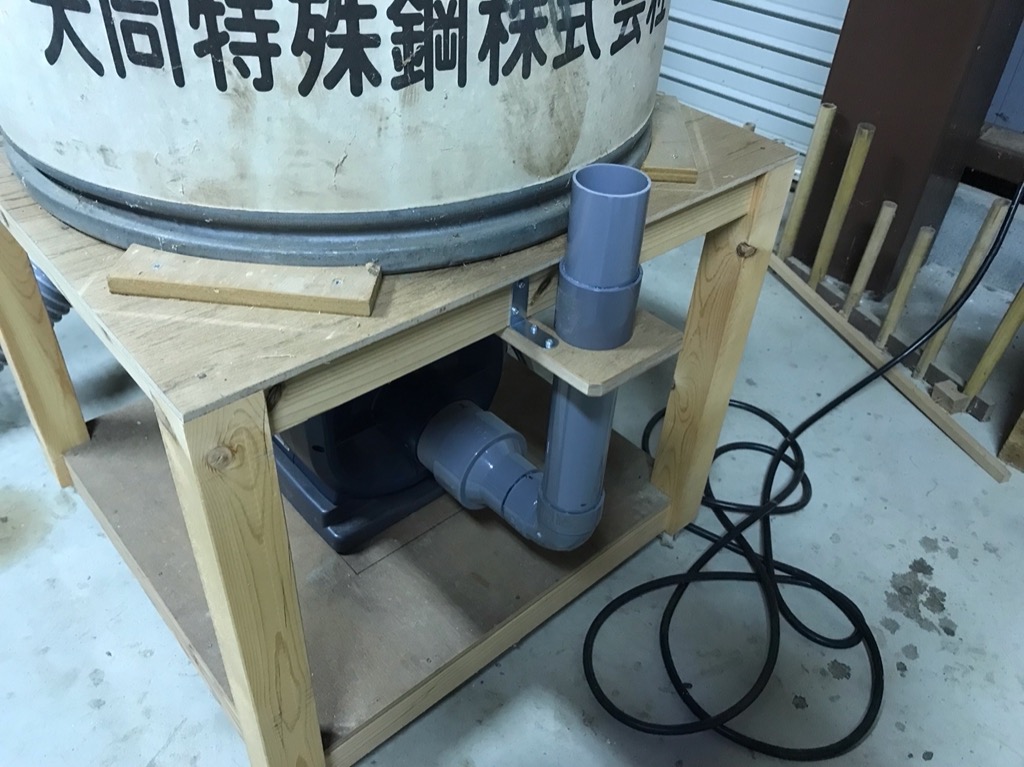
アウトレット管をサイクロン装置側と集塵機側にしているは、ダストボックスに溜まった粉塵を取り出す際にアウトレット管を分割する必要があるためです。
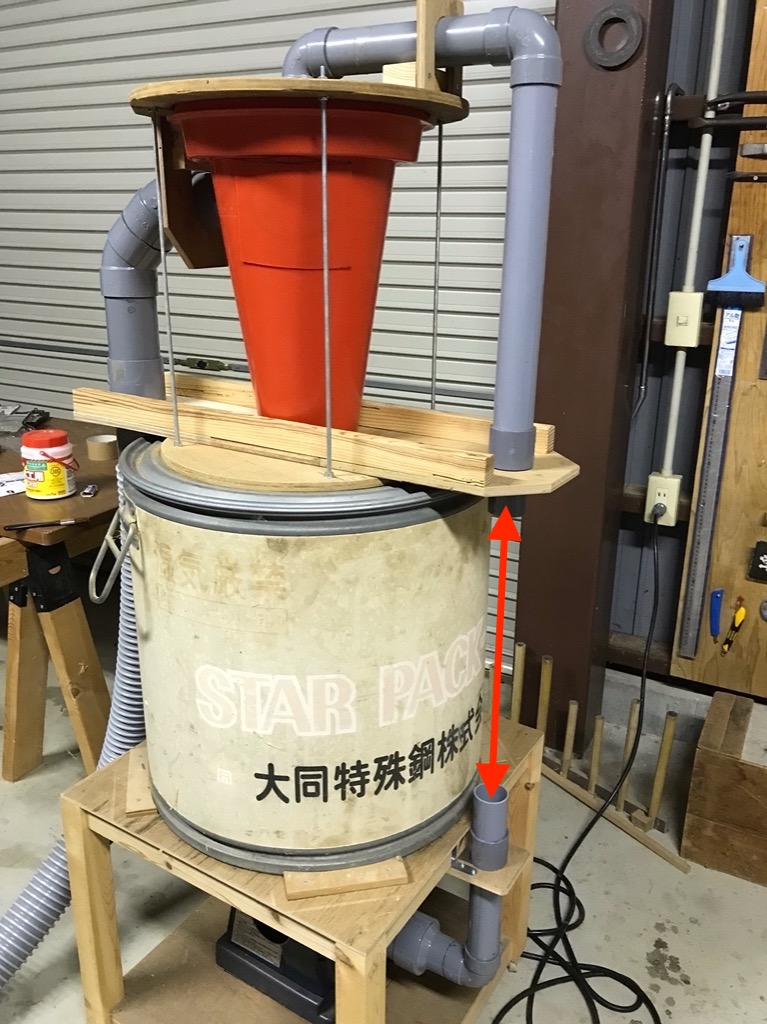
上写真で朱色矢印の長さを正確に測定。
その長さをもとに両端が受け口(ソケット)の脱着可能な配管部を作ります。
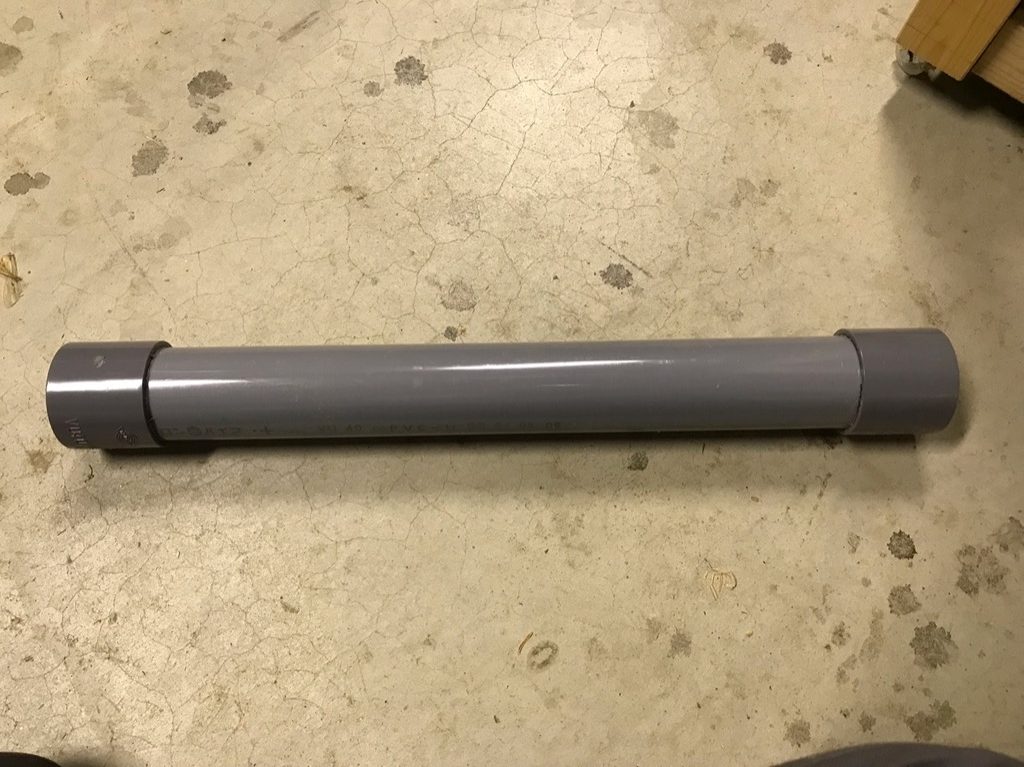
これを使ってサイクロン装置側と集塵機側とを繋ぎます(もちろん接着剤は使用しません)。
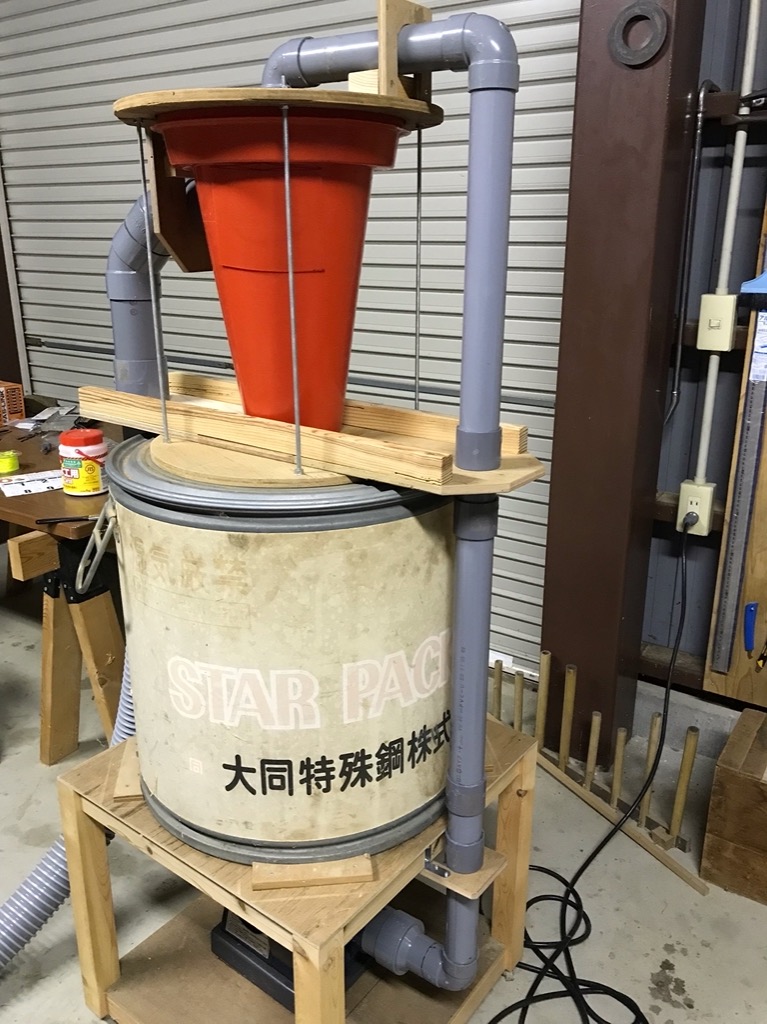
アウトレット管も完成し、これで全ての配管が完了したことになります。