自作サイクロン集塵機を改良することにし、前回、ダストボックス及び集塵機の設置台を作りました。
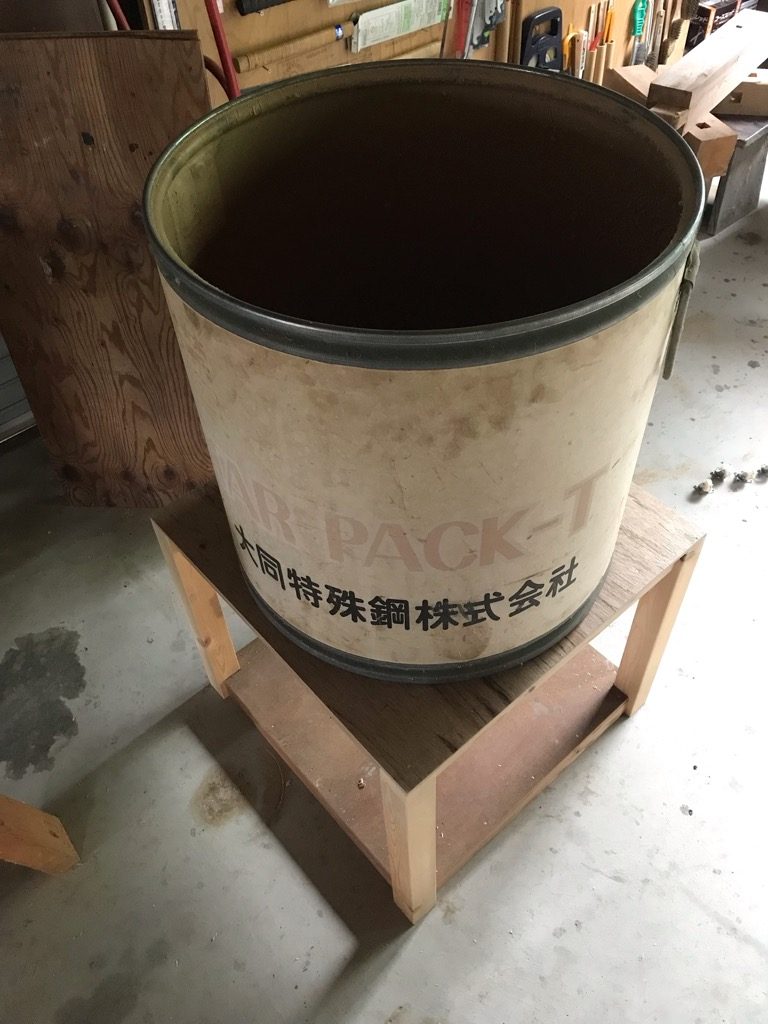
次にサイクロン装置本体の改良を行うことにします。
サイクロン装置の改良については、木工用集塵機のパワーに耐えられるように配管(インレット管及びアウトレット管)を変更するのがメインになります。
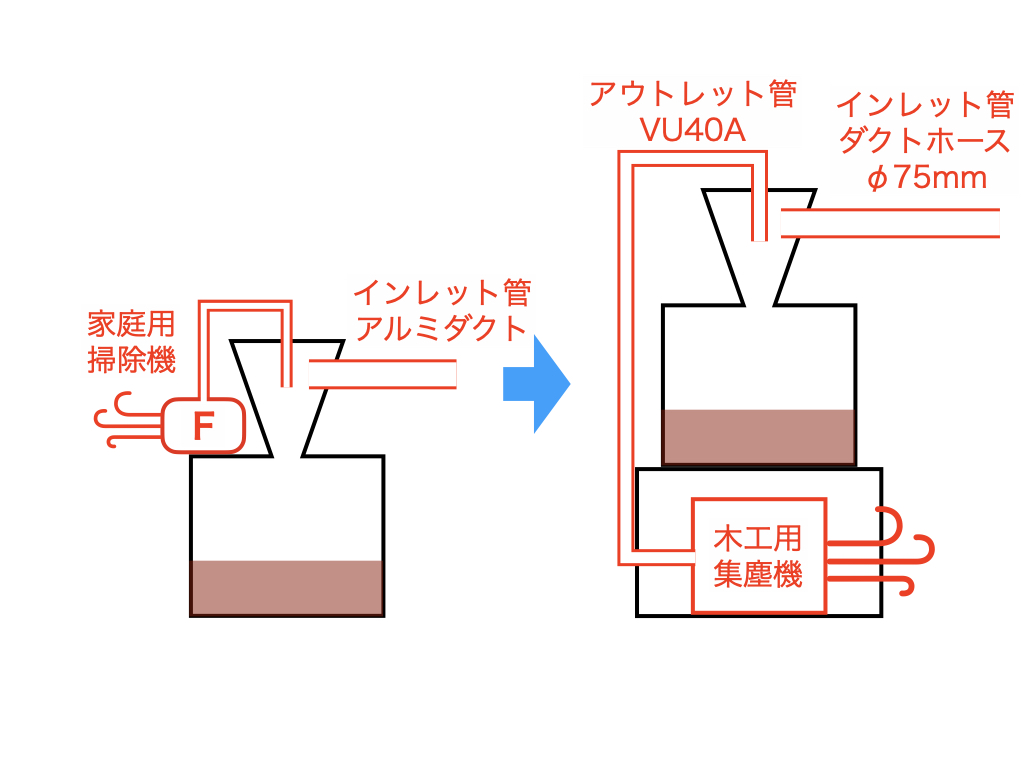
あと、これまでにサイクロン装置の出口(下写真でカラーコーンの下側)でおが屑が詰まることがあったため、この機会に出口の口径をφ100mmからφ120mmに大きくしておきます。
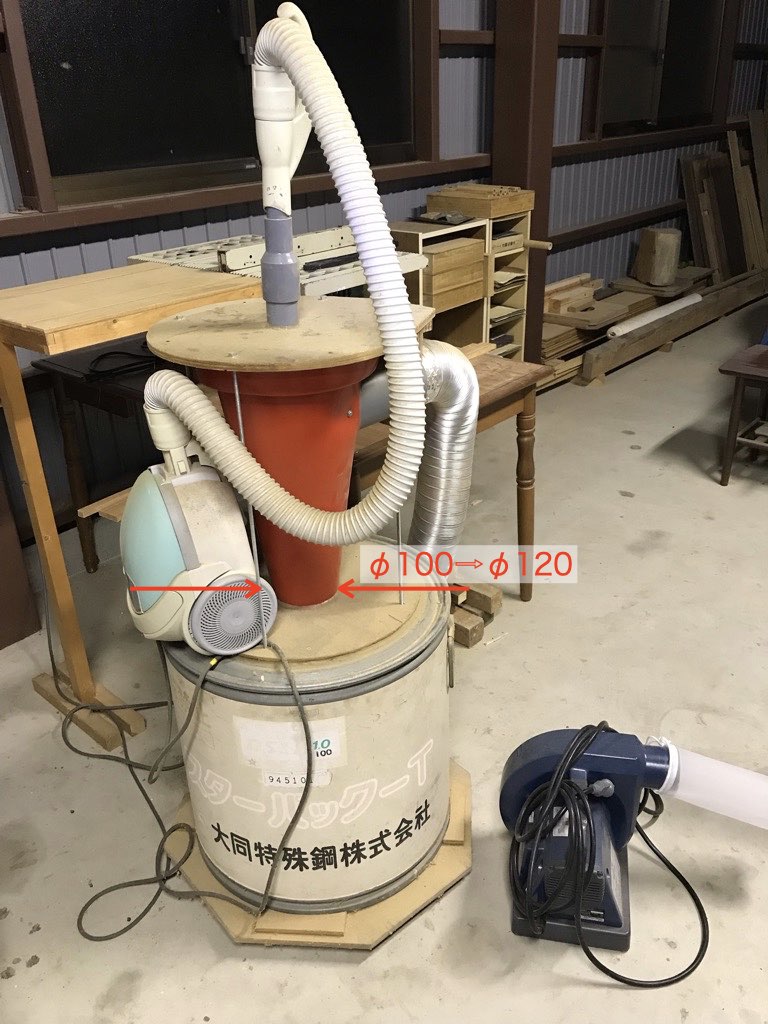
カラーコーンを支える合板を取り外し、自在錐で穴を大きく開け直そうとしたところ・・・
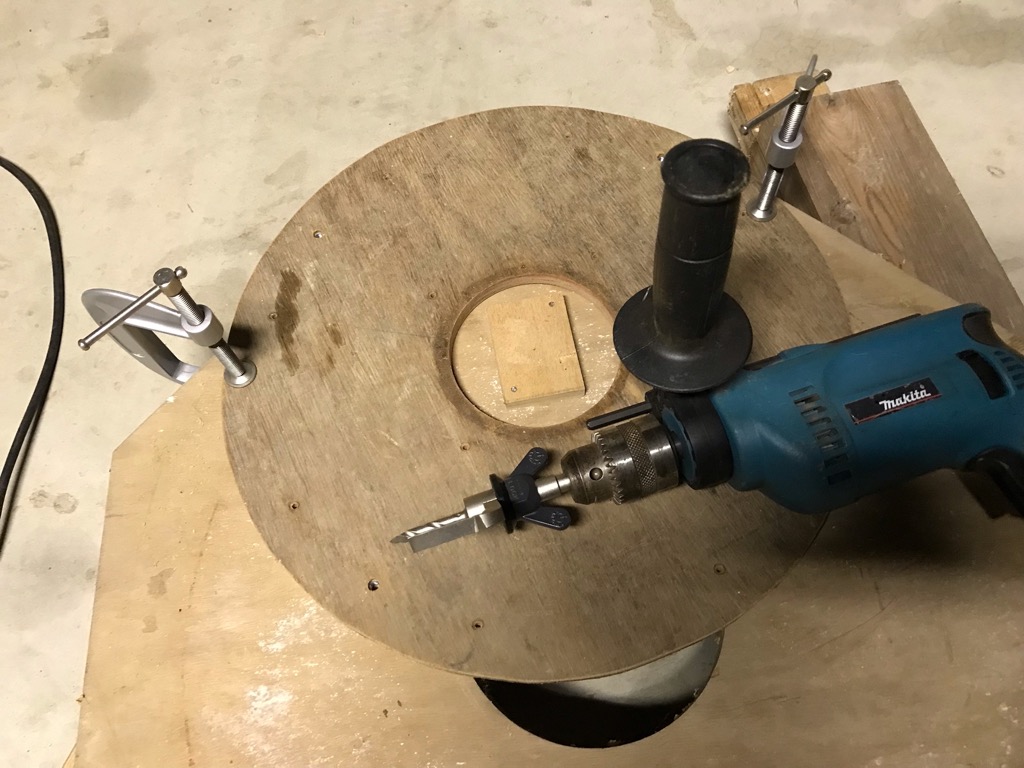
写真には撮っていませんでしたが、合板が古いこと(接着剤劣化)に加え、自在錐の切れ味が悪くて合板が無茶苦茶になってしまいました・・・。
そこで、自在錐の刃(焼き入れた鋼)をベンチグラインダーで研磨。
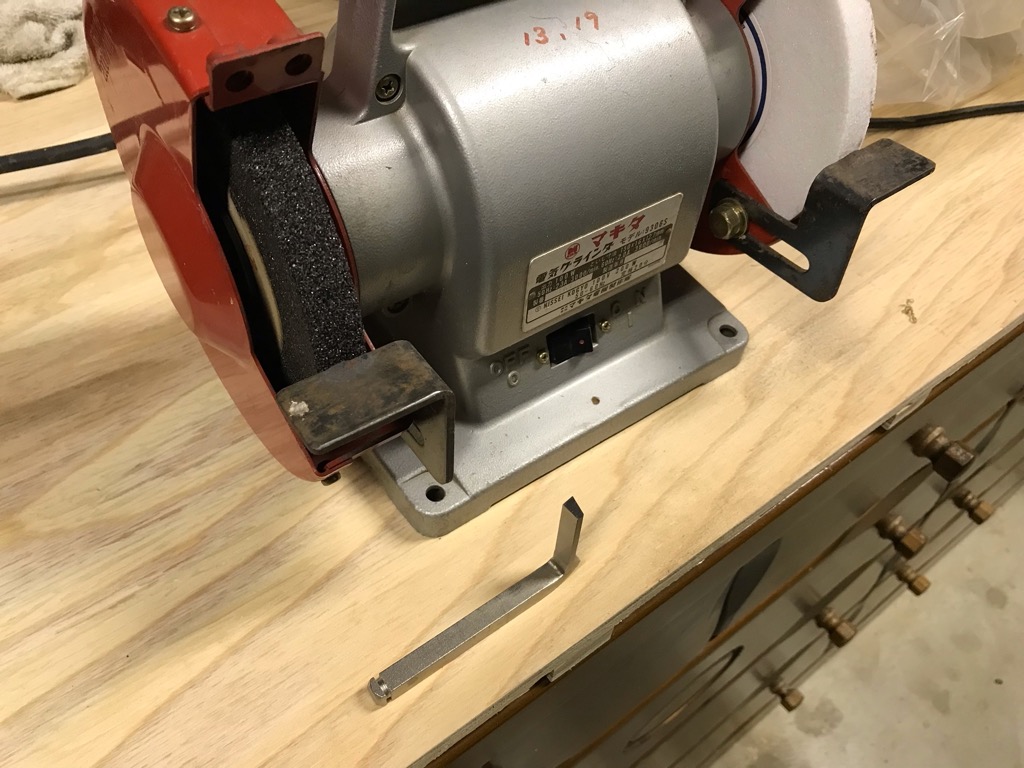
一応は研げていますが・・・
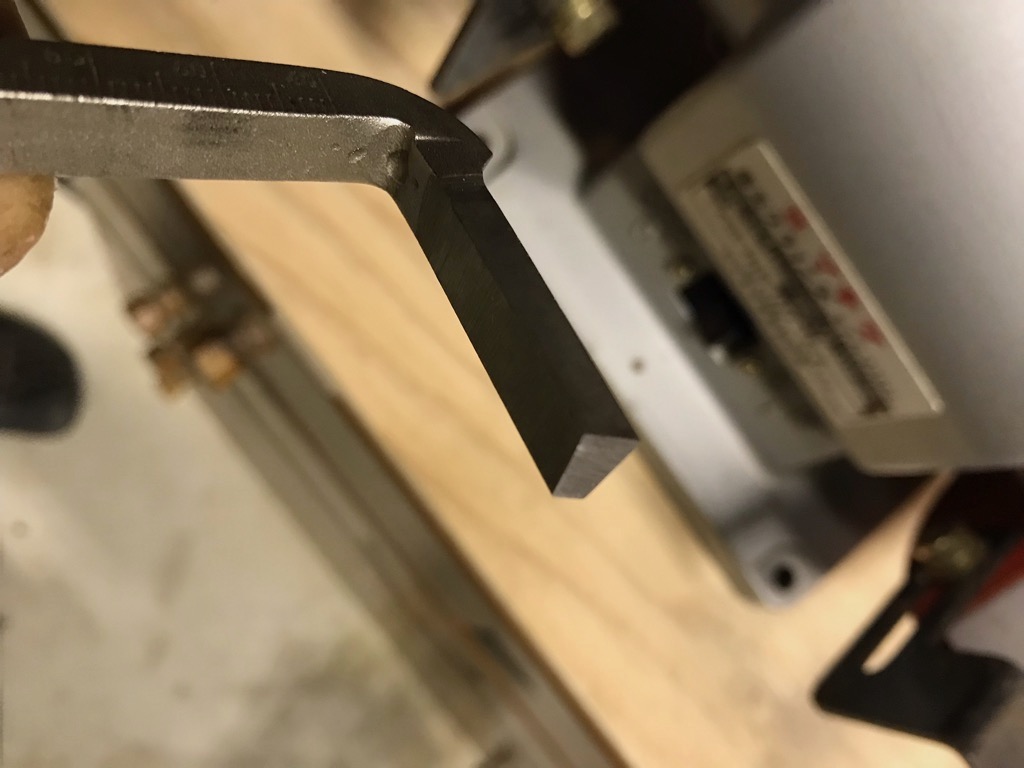
それが全く切れず、研磨前よりも悪くなる始末・・・
刃は付いているのですが、全然切れないのです。
試行錯誤するものの、結局、いつもお世話になっている研ぎ屋さんに泣きつくことに。
研いでもらったもので切断すると今度は新品以上の切れ味!さすがプロ!
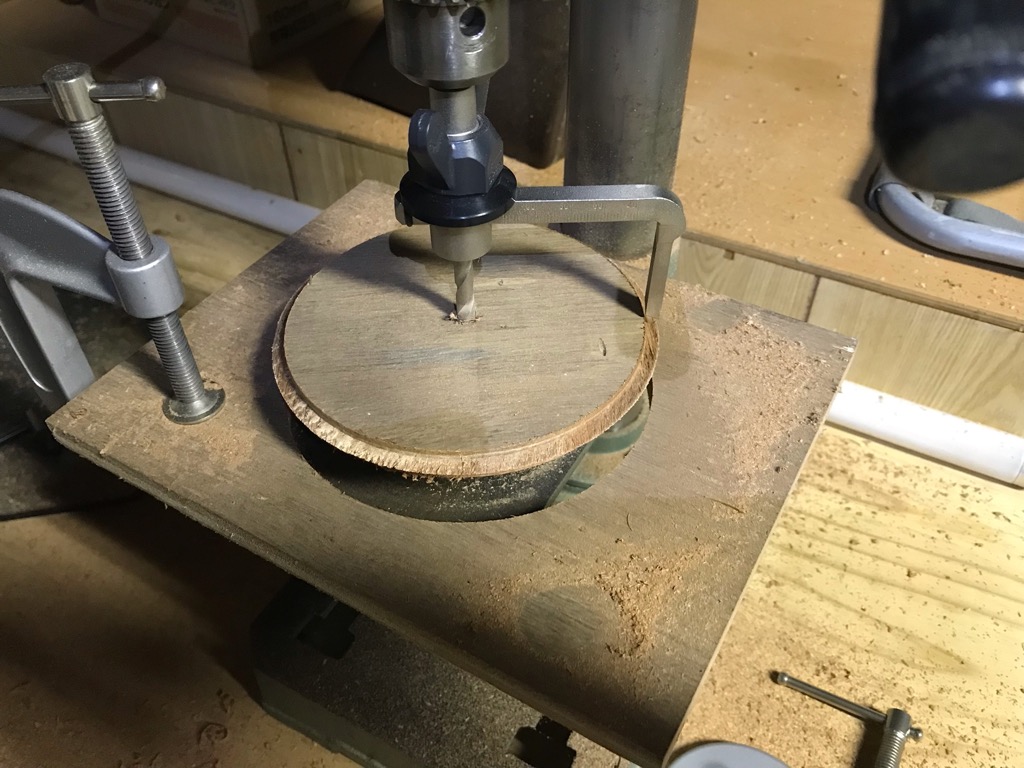
で、切れなかった原因ですが、刃角が全然違う向きに変わってしまっていたのです。
これでは切れるわけありませんが、研ぎ屋さんに指摘されるまで気が付きませんでした・・・。
今回、自在錐の研磨をお願いするついでに、いつも使っている鉈(両刃)も研いでもらいました。
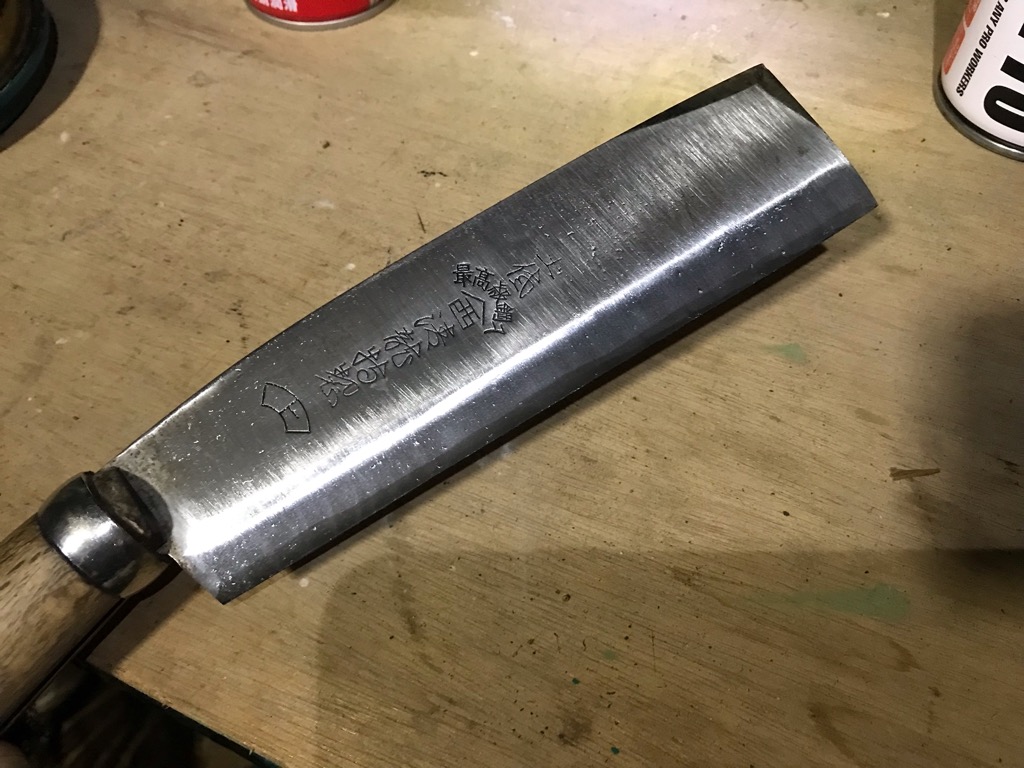
素晴らしい仕上がりです!
いつもは自分で研いでいるのですが、うまく研げていません。
何回かに一回はプロに研いでもらって修正してもらうが良さそうです。
さて、穿孔した板をカラーコーンに挿してみます(上が当初:φ100。下が今回:φ120)。

この板の位置を目印にしてカラーコーンの先端を切断します。
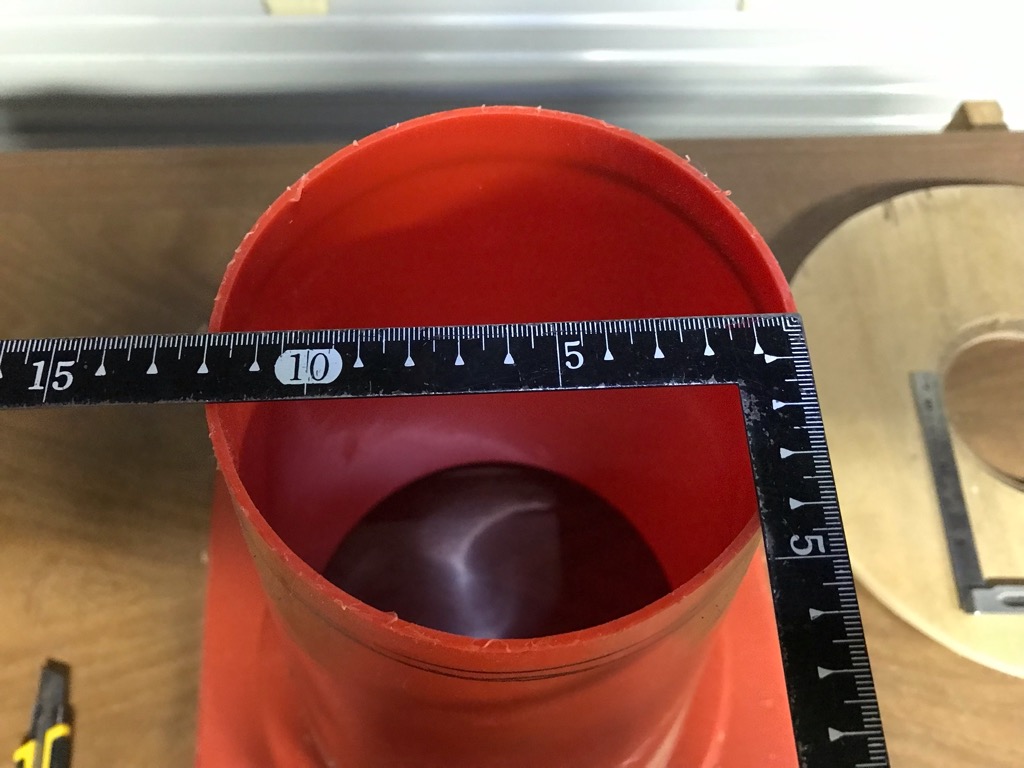
サイクロン装置出口の口径をφ100mmからφ120mmに拡大できました。
とりあえずダストボックスのうえに置いてみて、配管(インレット管&アウトレット管)の検討。
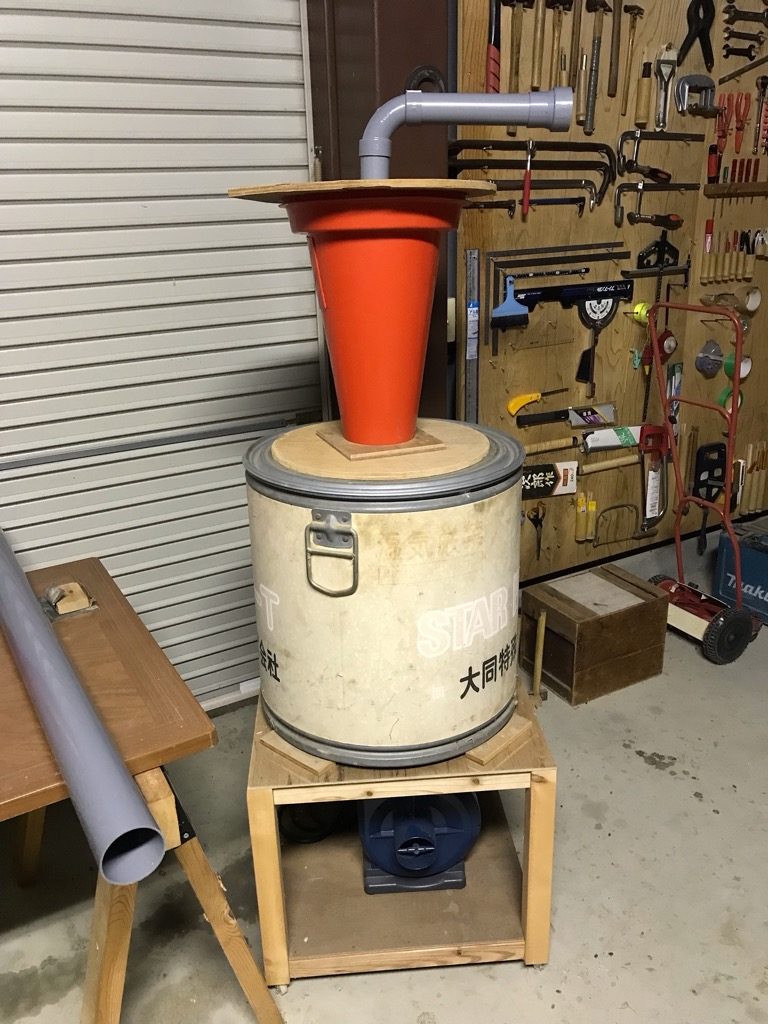
まずはインレット管(サイクロン装置への入り側)を配管することにします。
インレット管はφ75mmのダクトホース(下写真。EE型)を使うことにしています。
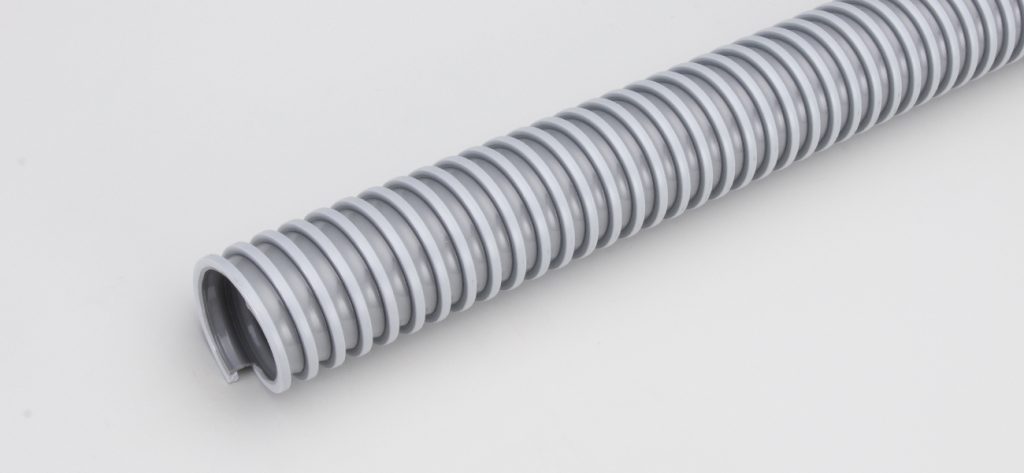
ダクトホースを直接サイクロン装置に取り付けるのは難しいため、塩ビ管を介すとともにダクトホースを脱着できるようにします。
塩ビ管の口径については、ダクトホースの内径が76.4mmであることから外径が76.0mmのVU65Aがちょうど良い具合です(塩ビ管にダクトホースを挿す形で簡易的に接続。本来はダクトホースのカフス等を使います)。
ただ、今回のように接続する場合、塩ビ管の肉厚分が抵抗になるため開先(内側)をテーパー状に切削しておきます。
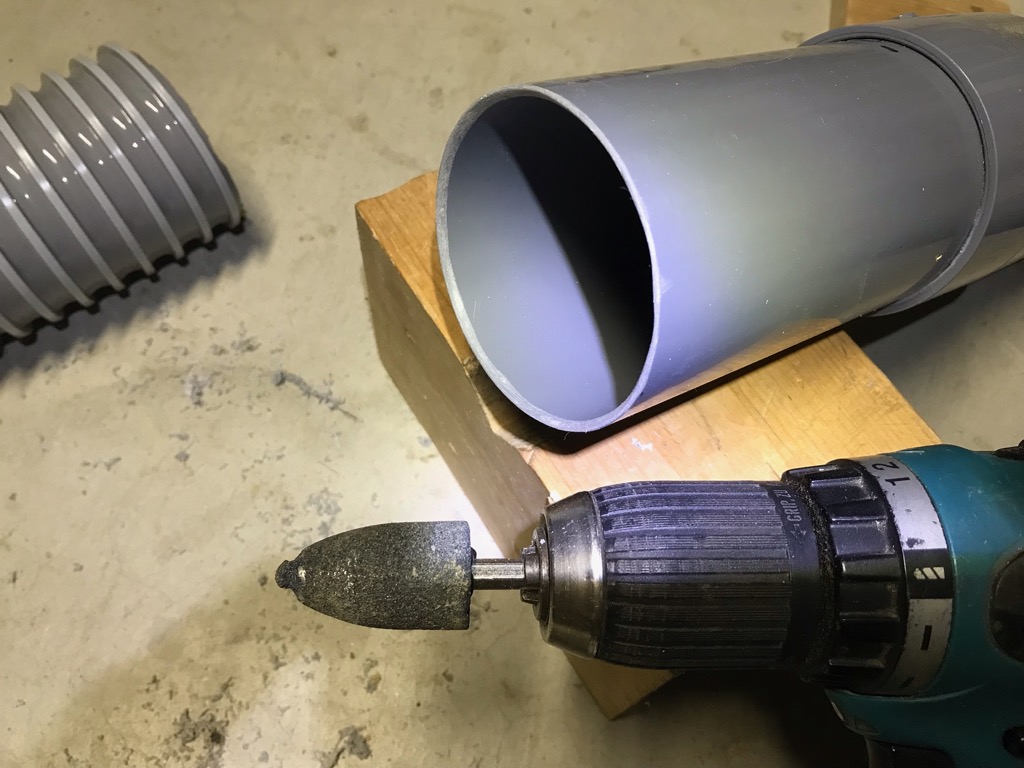
切削には百均の砲丸砥石を使用しました。
百均の砲丸砥石は砥石と軸がずれていてマトモに使える代物ではないのですが、こうした用途であれば十分役に立ちます。
そして、塩ビ管の継ぎ手(エルボ、ソケット)を使って下写真のとおり配管。
配管は井戸や薪ボイラーの工事で随分と慣れたためお手のものです(塩ビ管は扱いやすいです)。
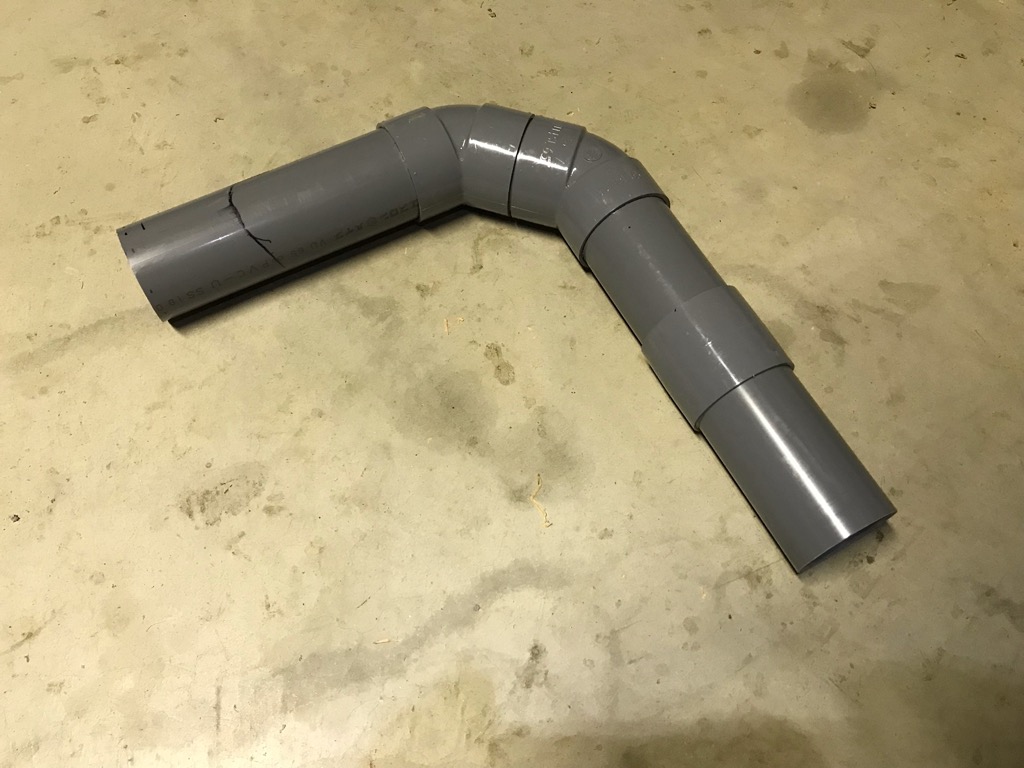
曲がり部分については90°エルボを使う手もありますが、インレット管(おが屑を送る)のため抵抗が小さくなるように45°エルボを2個使っています。
この塩ビ管にダクトホースを接続することになりますが、ダクトホースは以前使用していたアルミダクトと違って重量があります。
その力がサイクロン装置にかからないよう、下写真のとおり配管の途中にソケットを入れてインレット管を支えることにします。
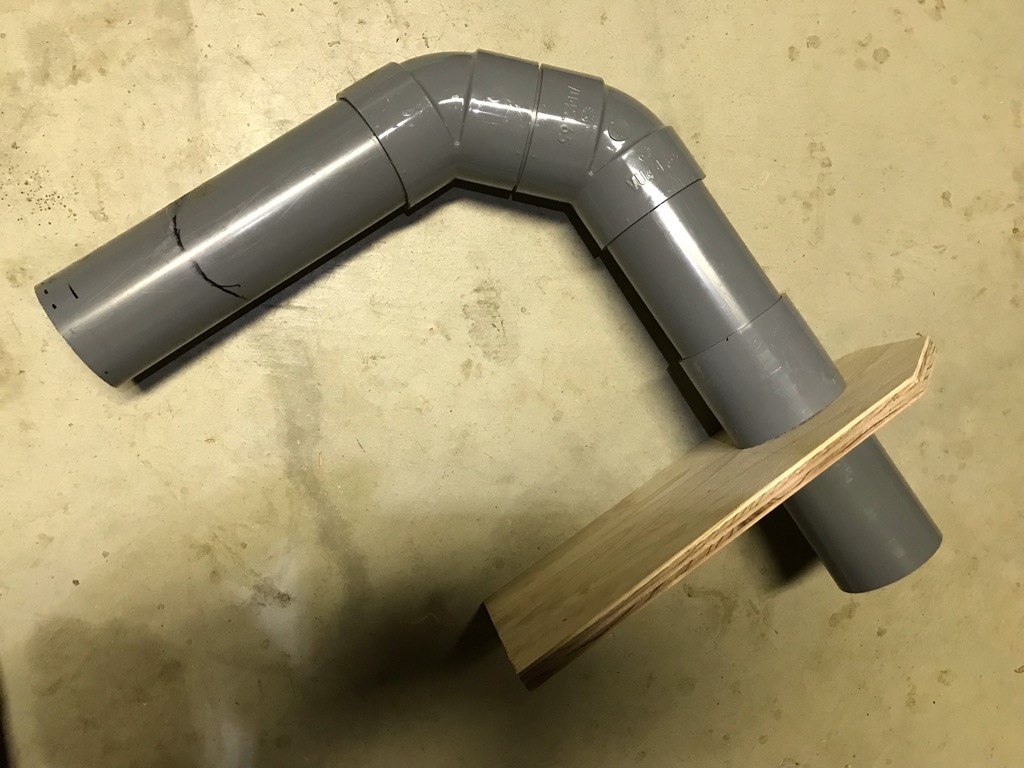
カラーコーンに穴(φ76mm)をあけてインレット管を取り付けます。
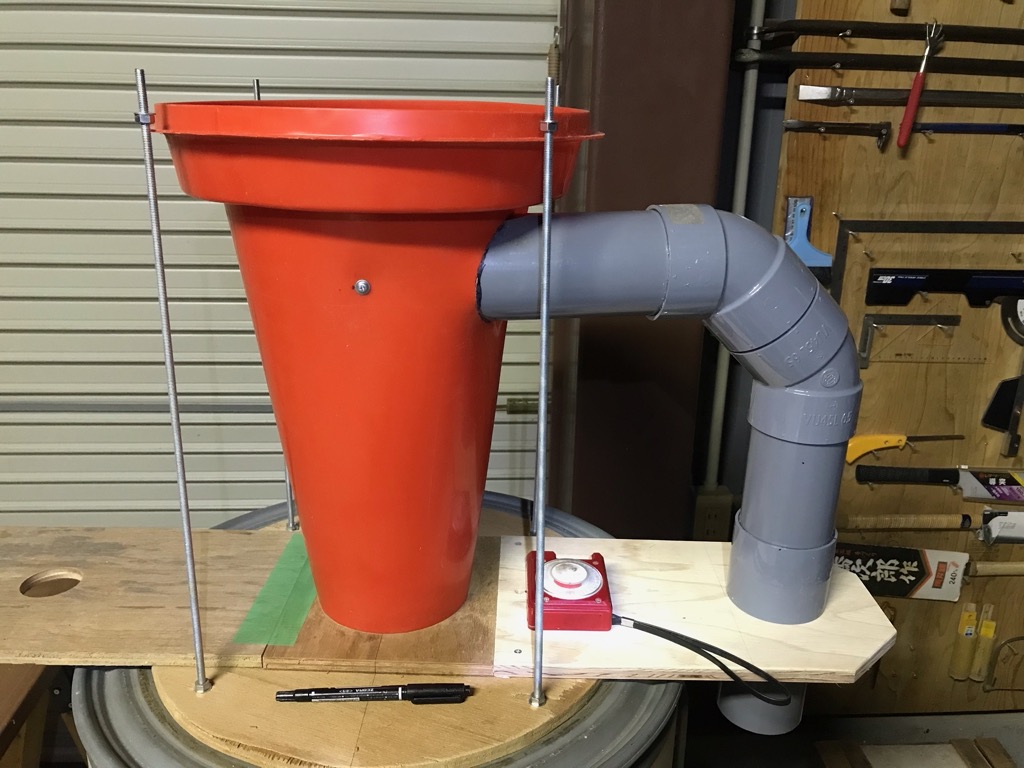
サイクロン集塵の仕組みから、インレット管の排出口をカラーコーンの側面に沿わせておくことが重要になります。
下写真のようにボルト・ナットで固定しておくと排出口の位置が安定します。
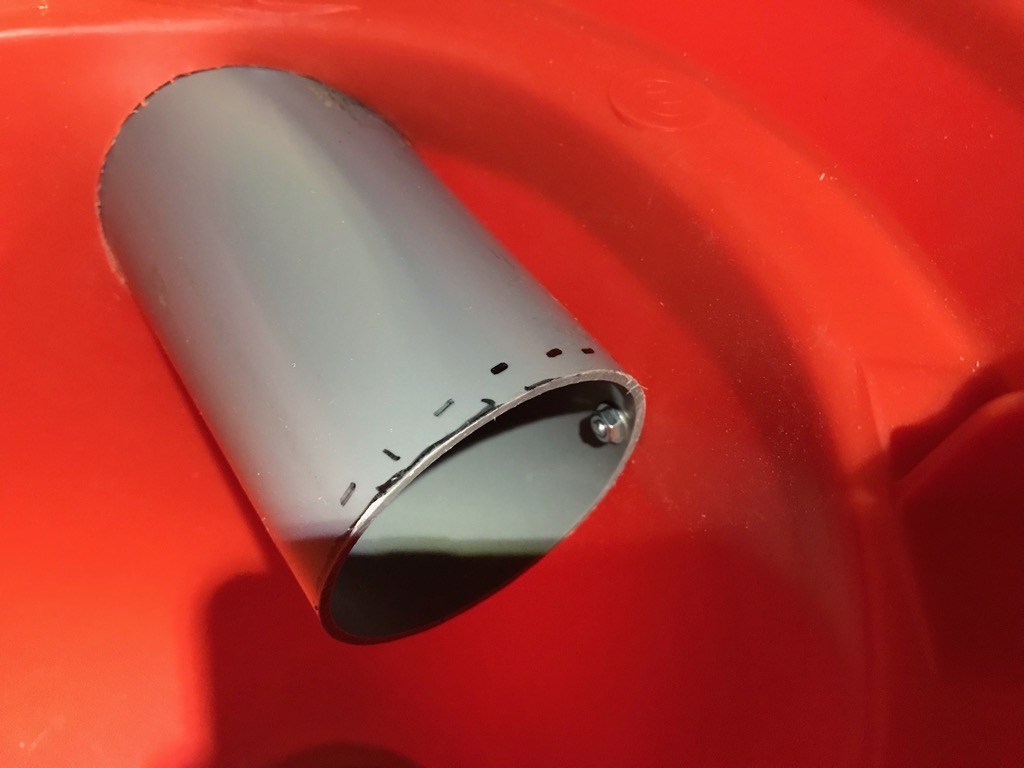
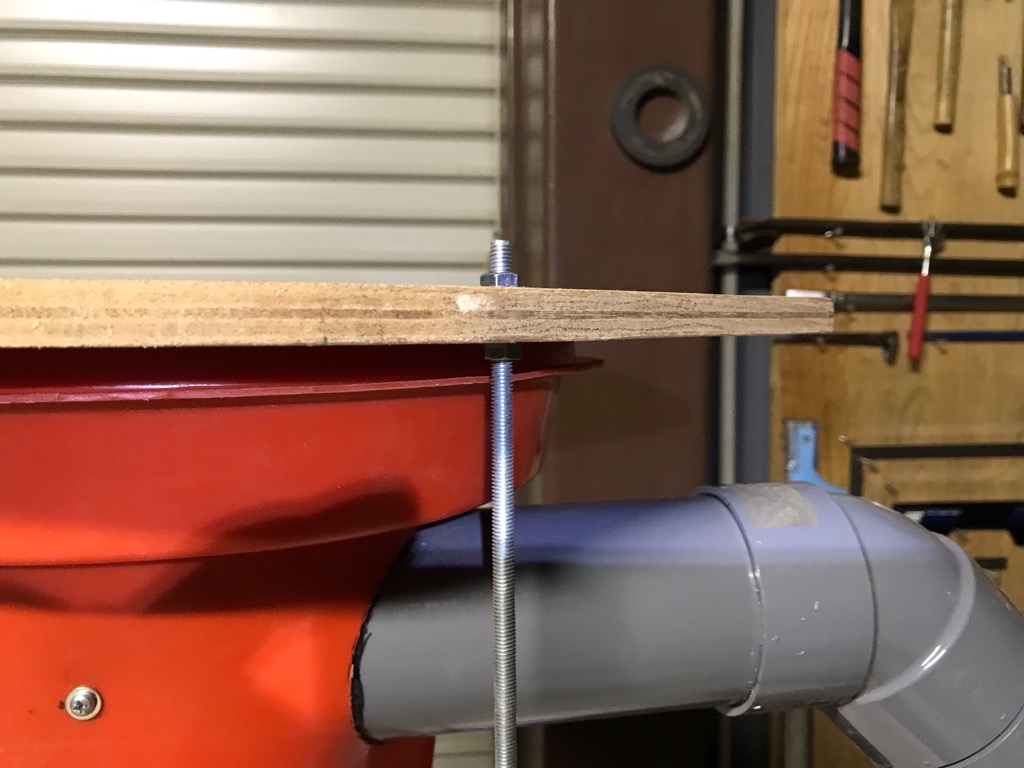
とりあえず、インレット管の配管完了です。
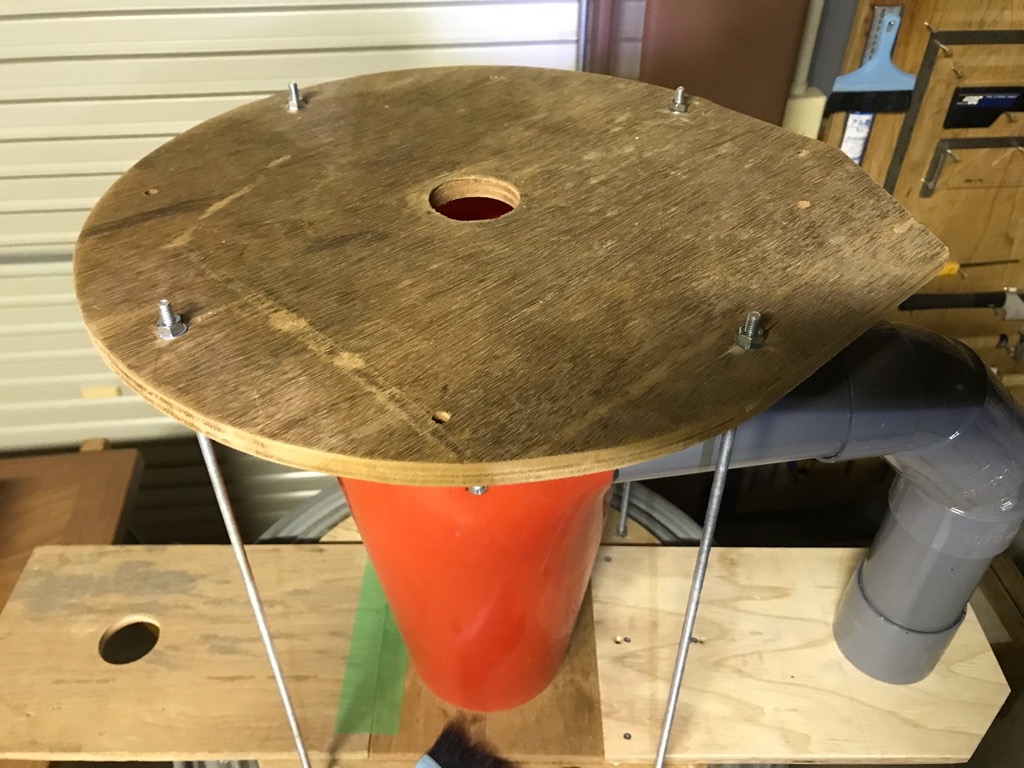
<続きます>